風電行業(yè)大型齒輪箱加工中的平齒機技術(shù)突破
隨著風電機組向大兆瓦方向發(fā)展,齒輪箱作為傳動部件,對加工精度和可靠性提出了更高要求。近年來,平齒機(平面齒輪加工機床)技術(shù)在多領(lǐng)域?qū)崿F(xiàn)突破,顯著提升了大型齒輪箱的制造水平。
1. 高精度加工與動態(tài)補償技術(shù)
新型平齒機采用多軸聯(lián)動數(shù)控系統(tǒng)與高剛性床身設(shè)計,結(jié)合激光干涉儀實時監(jiān)測技術(shù),實現(xiàn)加工誤差動態(tài)補償,齒面精度可達ISO 1328-3標準的3級水平。例如,通過熱變形補償算法,可抵消大型工件(直徑超5米)在連續(xù)加工中的微米級形變,確保齒距累積誤差≤15μm。
2. 智能化工藝優(yōu)化
基于數(shù)字孿生技術(shù)構(gòu)建的虛擬加工系統(tǒng),可提前模擬齒輪加工過程中的切削力分布和刀具磨損模型,優(yōu)化切削參數(shù)(如進給速度、切削深度)。某頭部企業(yè)應(yīng)用該技術(shù)后,加工效率提升30%,刀具壽命延長40%,單臺10MW齒輪箱加工周期縮短至72小時。
3. 復(fù)合加工能力突破
集成車削-銑削-磨削功能的復(fù)合平齒機實現(xiàn)"一次裝夾全工序加工",通過模塊化刀庫配置可完成行星輪、太陽輪等復(fù)雜構(gòu)件的連續(xù)加工。某6.2米行星輪加工案例顯示,同軸度誤差降低至0.01mm,加工振動幅度減少60%,顯著提升齒輪箱NVH性能。
4. 超硬刀具與冷卻技術(shù)創(chuàng)新
采用CBN/PCD涂層刀具配合微量潤滑(MQL)技術(shù),在加工42CrMo4等特種合金鋼時,切削速度提升至350m/min,表面粗糙度Ra≤0.4μm。新型內(nèi)冷式刀柄設(shè)計使切削液直達刀尖,有效控制加工溫度在±2℃波動范圍內(nèi)。
這些技術(shù)突破使平齒機加工大型齒輪箱的MTBF(平均故障間隔時間)突破8000小時,推動風電齒輪箱功率密度提升至15kW/kg以上,為20+MW級風電機組發(fā)展奠定技術(shù)基礎(chǔ)。未來隨著AI工藝自學習和超精密傳感技術(shù)的深度融合,平齒機將向"制造"目標持續(xù)邁進。
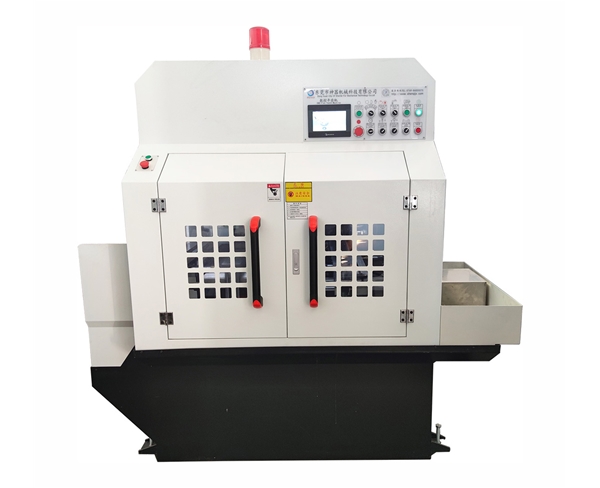
下一條:平齒機安全操作十大禁令